The Process of Custom Designing a Heavy Duty Overhead Crane
- charlespsnow
- May 22
- 5 min read
Heavy duty overhead cranes are indispensable in industries that demand the lifting and movement of extremely heavy loads. These cranes are the backbone of steel mills, shipyards, power plants, mining operations, and large manufacturing facilities, where safety, precision, and reliability cannot be compromised. Unlike standard cranes, heavy duty overhead cranes often require custom design to meet the unique operational challenges of each facility.
In this article, we will walk through the comprehensive process involved in the custom design of a heavy duty overhead crane, from initial consultation to after-sales support, highlighting the key technical and practical considerations at every stage.
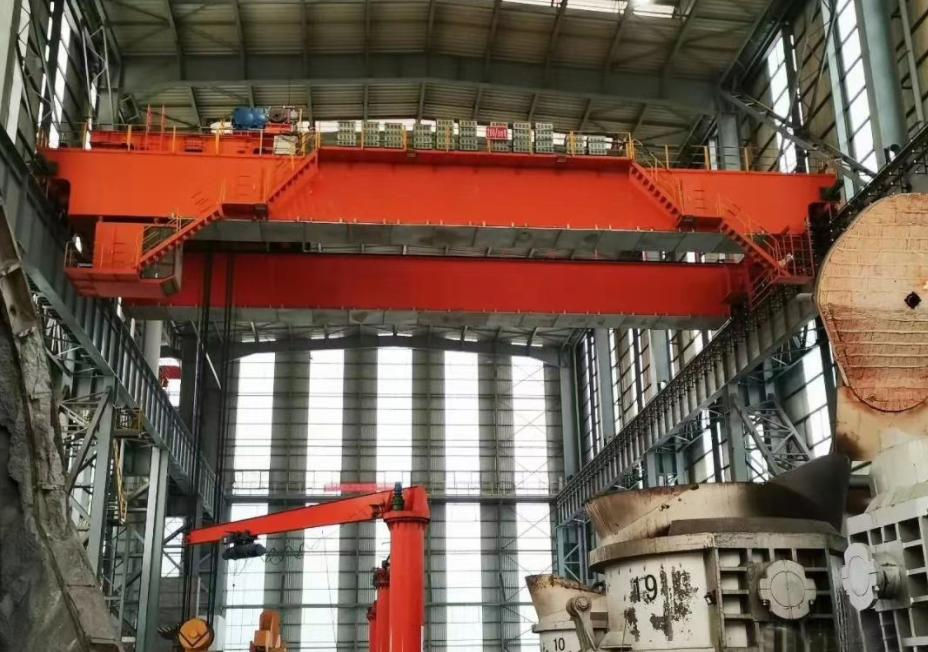
Understanding the Need for Custom Heavy Duty Overhead Cranes
Standard cranes are often mass-produced with fixed specifications that fit common industrial applications. However, when dealing with very large or heavy loads—often ranging from 50 tons up to 500 tons or more—the specific demands of the working environment, material handling, and operational frequency mean that a one-size-fits-all approach is insufficient.
Custom heavy duty cranes are engineered to:
Handle unique load types, shapes, and weights safely and efficiently
Fit within the physical constraints of the workspace or factory building
Operate reliably under demanding environmental conditions (such as extreme temperatures, humidity, or corrosive atmospheres)
Incorporate advanced safety and automation features for complex operations
Integrate with existing infrastructure like rails, conveyors, or production lines
The design and manufacturing process must therefore be highly tailored and precise.
Step 1: Initial Consultation and Detailed Requirements Analysis
The custom crane design process begins with a thorough needs assessment. This stage involves close collaboration between the overhead crane manufacturer engineering team and the client’s project managers, plant engineers, or safety officers.
Key aspects analyzed during consultation include:
Lifting capacity requirements: Determining the maximum weight and typical load distribution is fundamental. Heavy duty cranes can vary widely, from 50 tons to several hundred tons. Precise load data influences everything from structural design to motor specifications.
Span and lifting height: The horizontal distance between runway beams (span) and the vertical height needed to lift loads affect crane girder size and hoist mechanisms.
Duty cycle and operational frequency: The classification of crane service (e.g., A5, A6 according to FEM or ISO standards) reflects how often and intensively the crane will be used. This impacts component durability and motor selection.
Building and site conditions: Available space, building height, foundation strength, and existing infrastructure influence design constraints.
Environmental conditions: Temperature extremes, humidity, dust, explosive atmospheres, and exposure to chemicals all affect materials and protection measures.
Control preferences: Whether the crane will be operated via ground pendant, radio remote control, or cabin controls is decided here, alongside safety interlocks and automation needs.
A site survey is often performed to gather precise measurements and observe workflow, ensuring the crane design integrates seamlessly.

Step 2: Preliminary Design and Engineering Analysis
With detailed requirements, the engineering team begins the preliminary design phase. This involves:
Selecting crane configuration: Double girder overhead crane for sale is typically favored for heavy duty applications due to their strength and stability. The choice between top-running or underhung designs depends on the building structure.
Structural design: Engineering calculations ensure that the crane girder, end trucks, and runway beams will safely support the specified loads. Finite Element Method (FEM) software is widely used to simulate stresses, deflections, and dynamic forces.
Hoist and trolley selection: Based on load weight and lift height, appropriate hoisting mechanisms (wire rope or chain hoists) and trolleys are selected. For heavy duty cranes, open winch hoists with robust gearboxes and motors are often used.
Deflection limits: Excessive deflection in crane girders affects precise load handling. Calculations ensure deflection remains within industry standards for safety and performance.
Motor and drive systems: Motor power and speed are sized to meet lifting and trolley travel speed requirements, while ensuring efficient energy use.
Safety features: Overload protection, end stop buffers, anti-collision devices, and emergency brakes are incorporated into the design.
This phase results in detailed design drawings, load charts, and specifications that will guide fabrication.
Step 3: Component Customization and Procurement
Heavy duty overhead cranes often require specialized components that differ from standard cranes. The design team selects or customizes:
High-tensile steel girders: Fabricated with precision welding techniques for maximum strength.
Heavy-duty wire ropes and hoists: Designed to handle frequent use under extreme loads.
Advanced braking systems: Hydraulic or electromagnetic brakes with redundancy for safety.
Anti-sway and positioning systems: To improve load stability and reduce cycle times.
Control systems: Programmable logic controllers (PLC), variable frequency drives (VFD), and human-machine interfaces (HMI) customized to client needs.
Electrical components: Designed for industrial environments, with IP ratings for dust and moisture protection.
Manufacturers often source components from trusted suppliers or fabricate parts in-house to maintain quality control.
Step 4: Manufacturing and Quality Assurance
Manufacturing a custom heavy duty crane is a meticulous process governed by rigorous quality standards.
Key manufacturing steps include:
Steel fabrication: Cutting, shaping, and welding steel girders and end trucks. The welding process must comply with standards such as AWS D1.1 or ISO 3834.
Machining: Precision machining of wheels, shafts, gearboxes, and coupling parts.
Assembly: Pre-assembly of hoists, trolleys, and electrical cabinets in the workshop.
Surface treatment: Painting or galvanizing steel parts to protect against corrosion.
Load testing: Factory load tests are conducted at 125% or more of rated capacity to verify structural integrity and functional performance.
Electrical testing: Verification of wiring, control logic, emergency stop functions, and safety interlocks.
Documentation of all test results and certifications is provided to the client for compliance and traceability.
Step 5: On-Site Installation and Commissioning
Once shipped to the client site, the crane undergoes professional installation and commissioning. This is often the most challenging phase due to the size and complexity of heavy duty cranes.
Installation involves:
Assembling and securing runway rails if not already installed.
Hoisting and positioning the crane girders, end trucks, and trolleys using auxiliary lifting equipment.
Electrical hookup and integration with plant power supply.
Precision alignment of wheels and rails to ensure smooth operation.
Functional testing under no-load and load conditions.
Training crane operators on control systems, safety protocols, and emergency procedures.
Experienced installation engineers often work alongside client teams or provide remote technical support for successful commissioning.
Step 6: After-Sales Service and Long-Term Maintenance
The lifecycle of a heavy duty overhead crane extends far beyond installation. Continuous maintenance and after-sales service ensure operational safety and minimize downtime.
Typical services include:
Scheduled inspections and lubrication
Wear parts replacement (wire ropes, brakes, wheels)
Troubleshooting and remote diagnostics
Retrofitting or upgrading control systems for improved efficiency
Emergency repair support
A strong relationship with the crane supplier guarantees rapid response to issues and maximizes return on investment.
Conclusion
The custom design of a heavy duty overhead crane is a highly specialized, multi-stage process requiring deep engineering expertise and close client collaboration. From the initial assessment to manufacturing, installation, and maintenance, every step focuses on delivering a crane solution tailored to exact load handling needs while prioritizing safety, durability, and performance.
For industries handling extreme loads or complex lifting operations, investing in a custom-designed heavy duty overhead crane is essential to streamline workflows, protect personnel, and maintain productivity. Partnering with an experienced crane manufacturer ensures you get a solution engineered precisely for your application, backed by comprehensive support.
If you’re considering a heavy duty overhead crane for your facility, begin by consulting experts who understand the nuances of design and operation. The right crane can transform your material handling capabilities and provide reliable service for decades.
Comments