Advanced Load Monitoring Systems in Heavy Duty Overhead Cranes
- charlespsnow
- May 15
- 5 min read
Heavy duty overhead cranes play a critical role in industrial operations such as steel manufacturing, shipbuilding, construction, and logistics. These cranes are designed to lift and move extremely heavy loads—sometimes hundreds of tons—safely and efficiently. Ensuring safety and operational reliability in such demanding applications is paramount. This is where Advanced Load Monitoring Systems (ALMS) come into play, providing real-time data on load conditions and enhancing crane safety, performance, and lifespan.
This article explores the evolution, components, advantages, and future directions of advanced load monitoring systems used in heavy duty overhead cranes.
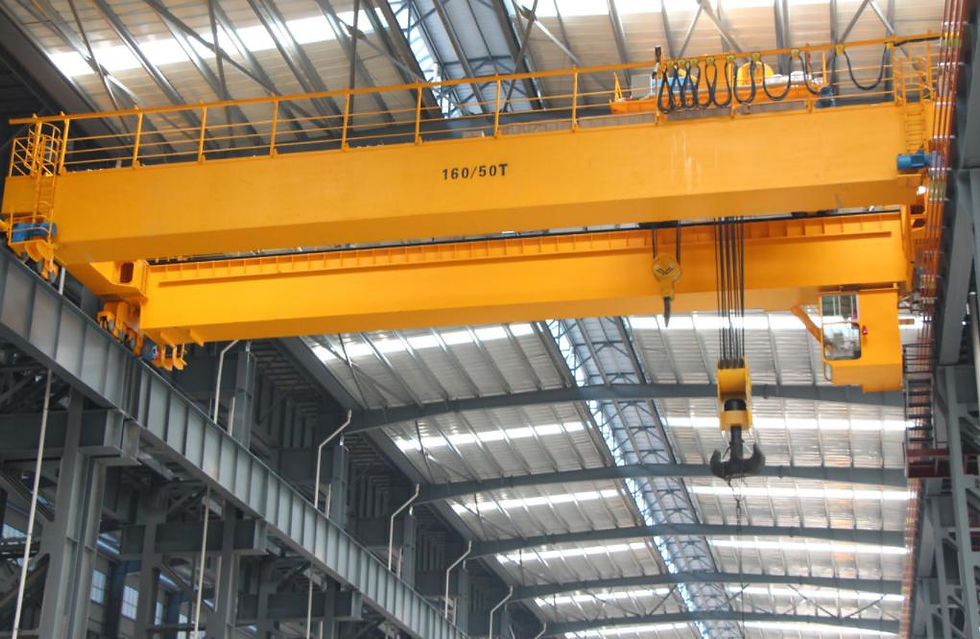
What Are Load Monitoring Systems?
Load monitoring systems are electronic systems integrated into cranes to continuously measure the actual load being lifted. Traditional cranes often rely on rated load charts and operator experience to avoid overload, but these approaches have limitations and risks. An advanced load monitoring system accurately measures the crane’s load in real time, detecting potential overloads, unbalanced loads, or unsafe conditions and alerting operators to prevent accidents.
Why Are Load Monitoring Systems Essential for Heavy Duty Overhead Cranes?
Heavy duty overhead cranes often handle massive and irregularly shaped loads. The risks associated with overload include:
Structural Damage: Excessive load can cause permanent deformation or catastrophic failure of crane components.
Safety Hazards: Overloading can lead to dropped loads, causing injury or death to personnel.
Operational Downtime: Damage and accidents result in costly downtime and repairs.
Legal and Compliance Risks: Most countries mandate safety measures for lifting equipment; advanced monitoring helps meet these requirements.
An advanced load monitoring system serves as a critical safeguard, improving operational safety and equipment longevity.
Core Technologies of Advanced Load Monitoring Systems
Modern load monitoring systems use various sensors and technologies to collect precise data:
1. Load Cells
Load cells are transducers that convert mechanical force into electrical signals. Installed between the crane hook and the lifting mechanism, load cells measure the tension in the hoist rope or chain. Types of load cells include:
Strain gauge load cells: Most common, using strain gauges bonded to metal that deform under load, changing electrical resistance.
Hydraulic load cells: Measure pressure changes in hydraulic fluid caused by load.
Piezoelectric load cells: Generate electric charge under mechanical stress, suitable for dynamic load measurement.
Load cells provide accurate, real-time load data critical for overload detection.
2. Rope Tension Sensors
In wire rope hoists, rope tension sensors measure the force on each rope strand, ensuring load balance. Unequal tension may indicate hazardous load swing or snagging.
3. Load Moment Indicators (LMI)
An LMI calculates the moment (torque) exerted on the industrial overhead crane structure by combining load and crane geometry data (e.g., boom angle, radius). It is especially useful for cranes with adjustable reach.
4. Tilt and Angle Sensors
These sensors detect crane boom or trolley inclination that could affect load distribution and stability.
5. Wireless Data Transmission
Many modern systems transmit load data wirelessly to operator cabins or control rooms, enabling remote monitoring and integration with crane control systems.
6. Integrated Control and Alarm Units
These units process sensor data to provide real-time feedback, trigger alarms, or automatically limit crane operation when unsafe conditions arise.

Features and Functions of Advanced Load Monitoring Systems
Beyond simple load measurement, modern systems offer numerous advanced features:
Real-time Load Display: Clear digital readout of the current load for operator awareness.
Overload Protection: Automatic alarms or control interventions when load limits are exceeded.
Load History Logging: Records of load data for maintenance and audit purposes.
Dynamic Load Monitoring: Detects sudden load changes such as shock loads or load swinging.
Load Distribution Analysis: Ensures balanced loads in multi-hook or dual-hoist cranes.
Operator Guidance: Provides warnings or suggested load adjustments.
Integration with PLCs and SCADA: Enables advanced automation and centralized crane fleet monitoring.
Self-diagnostics and Calibration: Ensures system reliability and accuracy over time.
Benefits of Advanced Load Monitoring Systems in Heavy Duty Overhead Cranes
1. Enhanced Safety
The most critical advantage is improved safety for crane operators and ground personnel. By preventing overloads and unstable load conditions, ALMS reduces the risk of accidents and catastrophic crane failures.
2. Prolonged Equipment Life
Consistently operating within design load limits avoids premature wear and structural damage, extending crane lifespan and lowering maintenance costs.
3. Increased Productivity
Operators can work with more confidence and precision, avoiding unnecessary load reductions or stoppages. Real-time data enables optimal load handling and crane performance.
4. Compliance with Regulations
Many international and national standards (such as OSHA, EN 13001, CMAA) require or recommend load monitoring for cranes. ALMS ensures compliance, reducing legal liability.
5. Data-Driven Maintenance and Operations
Load history data can be analyzed to predict maintenance needs, identify operator errors, or optimize load cycles, supporting condition-based maintenance strategies.
Challenges and Considerations
While advanced load monitoring systems bring significant benefits, some challenges exist:
Initial Cost: Installation of sophisticated sensors and control systems can be expensive, especially for retrofits.
Calibration and Maintenance: Load cells and sensors require periodic calibration and maintenance to maintain accuracy.
Environmental Conditions: Dust, moisture, vibration, and temperature extremes in industrial environments can affect sensor reliability.
Operator Training: Operators and maintenance personnel need training to understand and properly use load monitoring data.
Integration Complexity: Integrating ALMS with existing crane control and automation systems can be complex.
Despite these challenges, the long-term benefits generally outweigh the costs.
Future Trends in Load Monitoring for Heavy Duty Overhead Cranes
The development of load monitoring systems continues, driven by advances in sensor technology, data analytics, and automation:
1. Smart Sensors and IoT Integration
The use of Internet of Things (IoT) technology enables sensors to communicate load data to cloud platforms for real-time remote monitoring, analytics, and predictive maintenance.
2. AI and Machine Learning
AI algorithms can analyze load patterns, predict overload risks, detect operator errors, and optimize crane operation automatically.
3. Wireless and Non-Invasive Monitoring
Advances in wireless power and data transmission reduce wiring complexity, allowing easier installation and retrofit of monitoring systems.
4. Augmented Reality (AR) Support
AR devices can overlay load data and safety warnings onto the operator’s field of view, improving situational awareness.
5. Enhanced Integration with Automation
Future overhead cranes will increasingly incorporate ALMS with fully automated or semi-automated control systems, improving precision and safety in complex lifting tasks.
Conclusion
Advanced load monitoring systems are indispensable in the realm of heavy duty overhead cranes, enhancing safety, operational efficiency, and equipment longevity. Through the use of accurate sensors, real-time data processing, and smart control algorithms, these systems provide critical load information that helps prevent accidents, reduces downtime, and supports compliance with safety standards.
As industrial demands grow and crane technologies evolve, the adoption of sophisticated load monitoring systems will become even more widespread. Innovations in IoT, AI, and automation promise a future where overhead cranes operate with unprecedented safety, intelligence, and reliability—transforming how heavy lifting is managed across industries worldwide.
For companies investing in heavy duty overhead crane for sale, integrating an advanced load monitoring system is no longer optional but essential to safeguard personnel, assets, and operational success.
Comments