Custom-Built Rail Mounted Gantry Cranes for Intermodal Terminals
- charlespsnow
- Jul 9
- 4 min read
In today’s fast-paced global logistics landscape, intermodal terminals are under increasing pressure to move containers efficiently between rail, road, and maritime transport systems. To meet the growing demand for faster throughput, minimal downtime, and maximum safety, terminal operators are turning to custom-built rail mounted gantry (RMG) cranes. Unlike standard models, custom-engineered RMG cranes are tailored to meet the specific spatial, operational, and environmental requirements of each terminal, delivering unmatched flexibility, performance, and long-term value.
This article explores how custom-built RMG cranes are revolutionizing intermodal logistics, highlighting their design flexibility, operational benefits, and key features that make them indispensable for modern terminal operations.
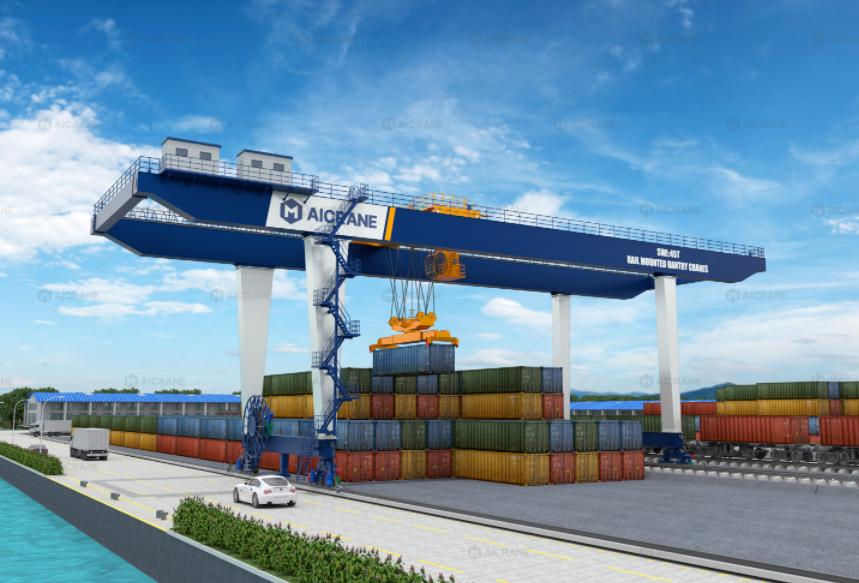
The Role of RMG Cranes in Intermodal Terminals
Rail mounted gantry cranes are a cornerstone of container handling at intermodal terminals, particularly those with rail yards integrated into the logistics flow. These rail gantry cranes straddle multiple railway tracks and container rows, efficiently handling containers between trains and storage areas or trucks. Their rigid rail-based system allows for high lifting capacities, precise movement, and efficient stacking — making them ideal for high-density container storage and rail-based loading operations.
Why Choose a Custom-Built RMG Crane?
While standard RMG cranes offer proven performance, they may not adequately address the diverse site conditions, operational goals, or environmental constraints of different terminals. Custom-built RMG cranes, on the other hand, are designed in collaboration with the terminal operator to align with specific use cases, such as:
Terminal layout (number of rail lines, span width, clearance height)
Container volume and stack configuration
Climate and wind load requirements
Integration with terminal operating systems (TOS)
Crane duty cycle and expected throughput
Specialized cargo handling (e.g., tank containers, swap bodies)
By tailoring the crane’s specifications and features, terminal operators can optimize space usage, streamline operations, and reduce energy consumption — resulting in a more sustainable and efficient logistics hub.
Key Advantages of Custom-Built RMG Cranes
1. Precision Engineering for Site Constraints
Custom-built RMG cranes can be designed to accommodate unique rail yard geometries and spacing between tracks. Whether your facility has three tracks or seven, a custom crane can be engineered with the exact span and clearance height to match. This adaptability ensures that even older or spatially constrained terminals can be modernized without expensive infrastructure changes.
2. Optimized Load Handling and Capacity
Depending on your operational needs, a custom crane can be designed with appropriate lifting capacity — from 40 tons to over 65 tons — and with single-lift or twin-lift spreaders for handling one or two 20-ft or 40-ft containers simultaneously. Additional features such as telescopic spreaders, rotating spreaders, and automatic positioning systems ensure faster and safer container transfers.
3. Higher Productivity Through Automation
Custom RMG cranes can be equipped with advanced automation and semi-automation technologies. These include:
Position detection systems
Anti-sway technology
Automatic gantry alignment
Remote control operation
Automation not only speeds up operations but also improves safety by minimizing human error and enabling round-the-clock operations with fewer operators.
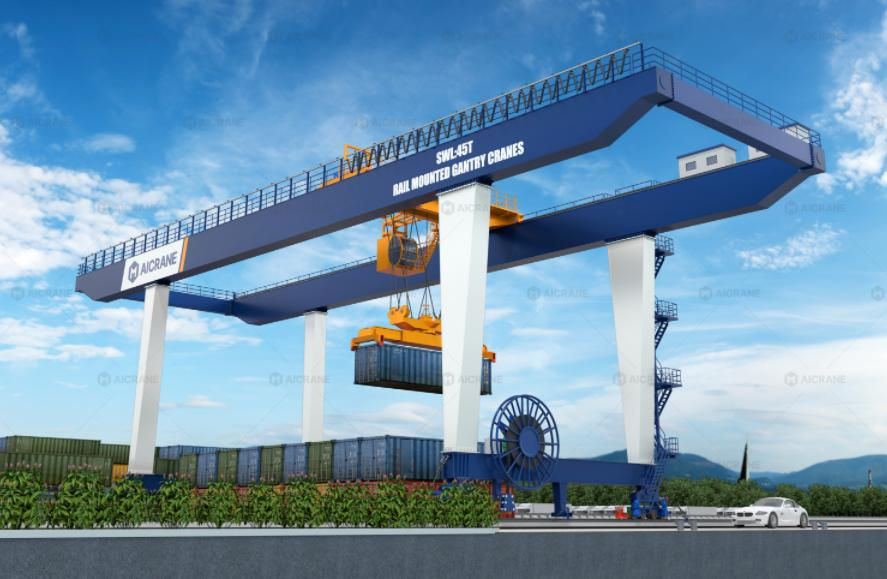
4. Enhanced Energy Efficiency and Sustainability
Modern intermodal terminals are increasingly committed to reducing their carbon footprint. Custom-built RMG cranes can incorporate energy-efficient technologies such as:
Regenerative drives that feed excess power back into the grid
LED lighting systems
Smart idle modes to reduce power consumption when not in use
Integration with renewable energy sources (e.g., solar-fed power systems)
Such custom options reduce operating costs and help terminals meet green port certifications or carbon reduction targets.
5. Robustness for Harsh Environments
If the terminal is located in an area with high winds, extreme temperatures, or corrosive sea air, a custom RMG crane can be fortified accordingly. Features may include:
High wind load resistance structures
Enclosed operator cabins with climate control
Stainless steel components or protective coatings
IP65-rated electrical enclosures for dust and moisture protection
This ensures the crane remains reliable and safe under all operating conditions.
Key Components and Custom Options
A custom-built rail mounted container gantry crane typically includes the following major components, with flexibility for modifications based on customer needs:
● Main Girder & Gantry Structure
Engineered to precise spans (typically 30–60 meters), the girder design is optimized for strength-to-weight ratio, corrosion resistance, and dynamic loads.
● Trolley and Hoist System
Customizable hoisting speeds, lifting height (often up to 18–22 meters), and spreader configurations are tailored based on handling requirements.
● Travel Mechanism
Equipped with high-quality motors and drives for smooth and accurate rail movement. Anti-collision and rail detection systems are included for safety.
● Operator Cab or Remote Station
Terminals can choose between a traditional onboard operator cabin or remote-control stations, with options for video monitoring and real-time data feedback.
● Electrical and Control Systems
Integrated with SCADA systems and TOS, allowing for real-time data collection, diagnostics, and performance optimization.
Case Study: Custom RMG Crane at a High-Volume Intermodal Terminal
A leading intermodal terminal in Central Europe faced challenges with container congestion and limited track spacing. By partnering with a crane manufacturer to develop a custom RMG crane with a 45-meter span, 16-meter lifting height, and semi-automatic twin-lift spreader, the terminal achieved the following improvements:
30% faster train unloading time
25% higher stacking efficiency
Energy savings of over 20% through regenerative drives
Improved safety with automated anti-sway and obstacle detection systems
This custom solution transformed the terminal into a high-efficiency logistics hub capable of handling future growth without expanding its footprint.
Customization Process: From Consultation to Commissioning
Investing in a custom RMG crane involves a collaborative design and engineering process, typically including:
Site AssessmentDetailed analysis of the rail yard, space constraints, throughput goals, and existing infrastructure.
Design Proposal2D/3D crane layout, simulations, and structural calculations presented for approval.
Engineering & FabricationManufacturing of the crane with precision to the approved design using high-quality materials.
Testing & DeliveryFactory load testing, pre-assembly checks, and shipment to the site.
Installation & CommissioningOn-site assembly and testing, along with operator training and system integration.
After-Sales SupportMaintenance packages, spare parts availability, and remote diagnostics support for long-term performance.
Conclusion
Custom-built rail mounted gantry cranes offer a strategic advantage for intermodal terminals striving for greater efficiency, adaptability, and sustainability. By tailoring the crane’s size, features, and automation level to match your exact terminal conditions, you not only improve day-to-day operations but also future-proof your logistics infrastructure.
Whether you’re upgrading an existing terminal or designing a new one from scratch, investing in a custom RMG crane ensures that your handling equipment aligns perfectly with your goals — delivering long-term value, safety, and performance.
Comments