Factors Influencing the Cost of a Steel Structure Warehouse
- charlespsnow
- Jun 10, 2024
- 4 min read
Steel structure warehouses have become increasingly popular due to their durability, flexibility, and cost-effectiveness. However, the cost of constructing such a warehouse can vary significantly depending on various factors. Understanding these factors can help businesses and investors make informed decisions and optimize their budgets. This article explores the primary factors that influence the cost of a steel structure warehouse.
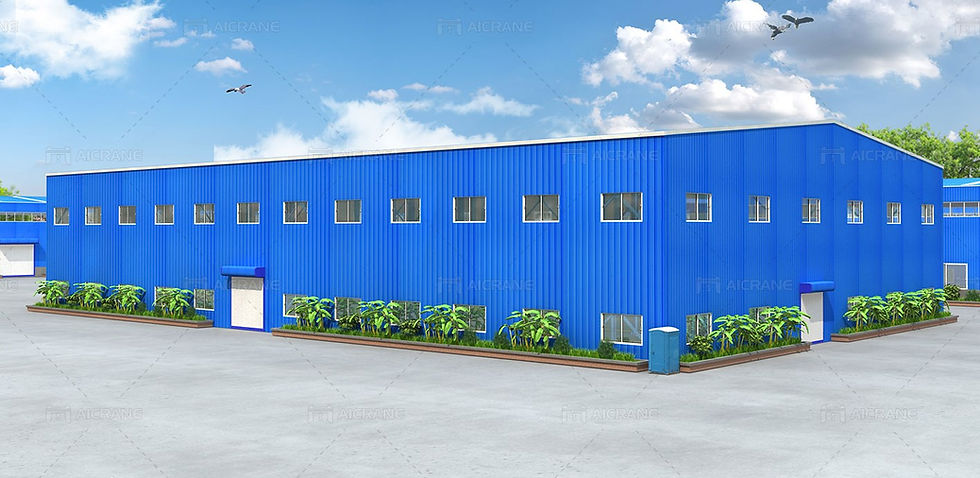
1. Design and Complexity
The design and complexity of the warehouse significantly impact the overall cost. A simple rectangular structure with minimal features will cost less than a complex design with multiple sections, mezzanines, or specialized areas. Customized designs that include unique architectural elements, curved shapes, or specific aesthetic requirements will require more materials and labor, thus increasing costs.
2. Size of the Warehouse
The size of the warehouse is one of the most obvious factors affecting cost. Larger warehouses require more materials and labor, which directly translates to higher costs. However, economies of scale can sometimes come into play, where the cost per square meter may decrease with the increase in size due to more efficient use of materials and labor.
3. Materials Quality and Type
The quality and type of materials used in the construction of the steel structure warehouse also play a crucial role in determining the cost. Higher-grade steel, which offers better strength and durability, will cost more than lower-grade options. Additionally, other materials such as insulation, roofing, cladding, and finishes can vary in quality and price. Opting for premium materials can increase the upfront cost but may result in lower maintenance costs and longer lifespan.
4. Location and Site Conditions
The location of the warehouse can significantly influence the cost due to factors such as local building codes, land prices, and site conditions. Urban areas with higher land prices will increase the overall cost. Additionally, site conditions such as soil type, topography, and accessibility can affect the foundation and construction methods required. Challenging site conditions may necessitate specialized foundation work or site preparation, adding to the cost.
5. Labor Costs
Labor costs can vary widely depending on the region and availability of skilled workers. In areas with high labor costs or a shortage of skilled workers, the construction cost will be higher. Conversely, regions with a readily available workforce may offer more competitive labor rates, reducing overall costs.
6. Construction Timeframe
The timeframe for completing the construction project can also impact the cost. Expedited projects may require additional labor shifts, overtime pay, and faster procurement of materials, all of which can increase costs. Conversely, longer construction periods can lead to higher indirect costs such as site management, equipment rentals, and potential disruptions.
7. Climate and Environmental Factors
Climate and environmental factors play a significant role in determining the design and materials required for the warehouse. Areas prone to extreme weather conditions such as heavy snowfall, strong winds, or earthquakes will require reinforced structures and specialized materials to ensure safety and compliance with building codes. These additional requirements can increase the overall cost.
8. Insulation and Energy Efficiency
The level of insulation and energy efficiency desired for the warehouse can also influence the cost. Higher insulation levels, energy-efficient windows, and HVAC systems can significantly add to the initial construction costs. However, these investments can lead to long-term savings in energy bills and improved environmental performance, making them worthwhile for many businesses.
9. Building Codes and Regulations
Compliance with local building codes and regulations is mandatory and can affect the cost of construction. Different regions have varying requirements for structural integrity, fire safety, accessibility, and environmental impact. Ensuring that the warehouse meets all regulatory requirements may involve additional design work, materials, and inspections, thereby increasing costs.
10. Future Expansion Plans
Considering future expansion plans during the initial design phase can influence the cost. Designing a warehouse with the potential for future expansion can be more cost-effective in the long run, even if it increases the initial construction cost. This approach can save significant expenses related to major modifications or extensions in the future.
11. Technology and Automation
The integration of technology and automation systems within the warehouse can also impact the cost. Advanced systems for inventory management, automated storage and retrieval, and building management can increase the initial investment. However, these technologies can enhance operational efficiency, reduce labor costs, and improve accuracy, offering long-term financial benefits.
12. Vendor and Contractor Selection
The choice of vendors and contractors plays a crucial role in determining the cost and quality of the warehouse construction. Reputable contractors with a proven track record may charge higher fees but can offer better quality workmanship, adherence to timelines, and fewer delays or issues. It is essential to balance cost considerations with the reliability and expertise of the contractor.
13. Financing and Economic Conditions
The overall economic conditions and financing options available can also influence the cost of constructing a steel structure warehouse. Favorable economic conditions, lower interest rates, and accessible financing options can reduce the financial burden on the project. Conversely, economic downturns or restrictive financing can increase costs due to higher interest rates and limited funding availability.
Conclusion
Constructing a steel structure warehouse involves numerous factors that can significantly influence the overall cost. By carefully considering design complexity, size, material quality, location, labor costs, construction timeframe, climate, insulation, building codes, future expansion, technology, vendor selection, and economic conditions, businesses can make informed decisions and manage their budgets effectively. While initial costs are important, it is also crucial to consider long-term benefits and operational efficiencies that can result from strategic investments in quality materials, design, and technology.
Comments