How Anti-Sway Systems Improve Safety and Efficiency in Container Gantry Crane Operations
- charlespsnow
- Jun 30
- 5 min read
In the world of port logistics and container handling, container gantry cranes play a critical role in the movement of heavy loads with speed and precision. Whether it's a ship-to-shore (STS) crane or a rail-mounted gantry (RMG) or rubber tyred gantry (RTG) crane, safety and efficiency are top priorities for crane operators and terminal managers. One of the most transformative advancements in this field is the implementation of anti-sway systems. These systems are designed to stabilize suspended loads during crane operation, greatly reducing sway caused by acceleration, deceleration, or environmental factors such as wind. In this article, we will explore how anti-sway systems work and how they enhance both safety and operational efficiency in container gantry crane operations.
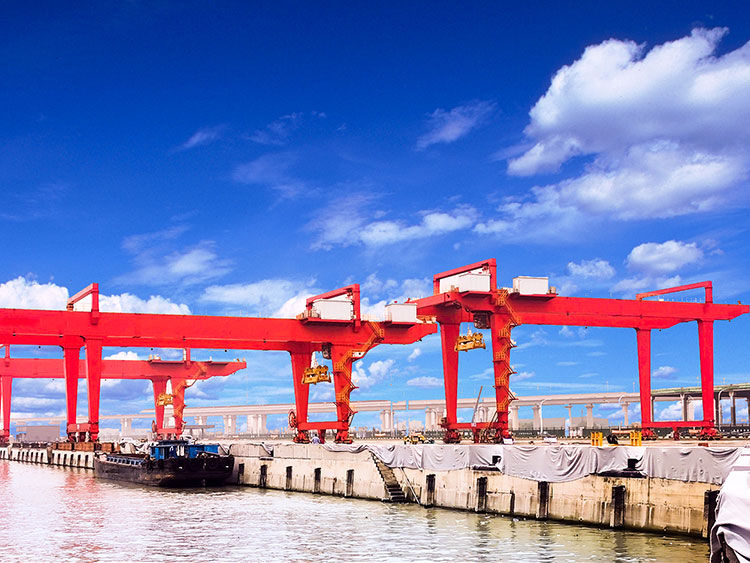
Understanding the Challenge: Load Sway in Gantry Cranes
When a container is lifted by a crane, it behaves like a pendulum. As the trolley or crane structure moves horizontally, the suspended load may start to sway due to inertia. This oscillation presents a number of operational challenges:
Safety hazards: Uncontrolled load sway can endanger workers on the ground and nearby equipment, increasing the risk of accidents.
Reduced productivity: Operators must often slow down or wait for the sway to settle before continuing, reducing operational speed.
Damage risks: Swaying containers can collide with other containers, crane structures, or cargo, causing equipment damage and financial loss.
Increased operator fatigue: Constant adjustments to compensate for sway increase mental and physical strain on crane operators.
Traditional crane operations relied heavily on operator skill to control sway manually. However, human limitations and environmental variables make perfect sway control extremely difficult. This is where anti-sway technology comes in.
What Is an Anti-Sway System?
An anti-sway system is a control technology integrated into the crane’s drive and control system to automatically suppress or compensate for pendulum-like motion of the load during movement. It uses real-time data from sensors and mathematical algorithms to adjust the crane’s acceleration and deceleration profiles, minimizing sway without human intervention.
There are two main types of anti-sway systems:
Passive Anti-Sway Systems: These include mechanical components such as dampers and pendulum limiters that reduce sway through physical design.
Active Anti-Sway Systems: These are software-driven systems that use feedback from sensors and apply counteracting forces or adjust movements to neutralize sway dynamically.
Most modern container gantry cranes employ active anti-sway control due to its precision and adaptability to different load conditions.
How Anti-Sway Systems Work
The heart of an active anti-sway system is its algorithm and feedback control loop. Here’s a simplified breakdown of how it operates:
Sensor Input: Sensors detect the position and angle of the load in real time.
Data Processing: The control system processes the input using predictive mathematical models to calculate the sway and its likely future behavior.
Motion Adjustment: Based on this data, the crane’s drive system adjusts the trolley or gantry motion (acceleration/deceleration curves) to counteract the sway.
Continuous Feedback: This loop continues as the crane moves, ensuring that any developing sway is corrected almost instantly.
Some systems also integrate with anti-collision and automation modules for further operational synergy.

Benefits of Anti-Sway Systems in Container Crane Operations
1. Enhanced Operational Safety
The most critical benefit of anti-sway technology is safety. By keeping the suspended load stable during movement, the system prevents erratic swinging that could cause:
Injury to ground personnel
Damage to stacked containers or equipment
Instability in the crane structure during high-speed operations
This is especially important in automated or semi-automated terminals, where human oversight is limited, and precision is paramount.
2. Improved Crane Efficiency and Productivity
With sway automatically controlled, crane operators can move loads faster and more confidently without waiting for sway to subside. This results in:
Faster cycle times: Containers are loaded and unloaded more quickly.
Reduced downtime: Operators don’t need to pause operations due to excessive sway.
Higher yard throughput: More containers are moved per hour, improving terminal efficiency.
In competitive port operations, even a few seconds saved per cycle can result in significant gains over time.
3. Reduced Operator Fatigue and Training Requirements
Manual sway control requires constant attention and skill, which can lead to operator fatigue and error. Anti-sway systems reduce this burden by automating part of the process. This allows:
Less experienced operators to work more effectively
Longer operation shifts with reduced physical strain
Easier training and onboarding of new staff
This is particularly valuable in regions facing skilled labor shortages or high operator turnover.
4. Lower Maintenance and Operational Costs
While installing anti-sway systems involves an upfront investment, they contribute to long-term savings through:
Reduced wear and tear on crane components due to smoother movements
Fewer accidents and associated repair costs
Less cargo damage, leading to lower insurance premiums and claims
Maintenance intervals can also be optimized due to less mechanical stress on the crane structure.
5. Better Performance in Automation and Remote Operations
Anti-sway systems are crucial for fully automated container terminals or remote crane operations, where there is no operator on-site to visually monitor and respond to sway. By integrating with automation software, anti-sway control ensures containers are placed accurately every time, improving the reliability of the entire logistics chain.
Applications Across Different Types of Container Cranes
Anti-sway systems are now widely implemented in various container gantry crane types:
Ship-to-Shore (STS) Cranes: Essential for high-speed loading/unloading of large container ships where sway is more pronounced due to long hoisting heights.
Rail-Mounted Gantry (RMG) Cranes: Improve precision and efficiency in intermodal rail yards, where space is limited and accurate container placement is vital.
Rubber Tyred Gantry (RTG) Cranes: Enhance mobility and control in container yards, especially when navigating narrow aisles or uneven ground.
Whether the crane is manually operated, semi-automated, or fully autonomous, anti-sway control enhances performance across the board.
Real-World Impact: A Case Example
A mid-size container terminal in Southeast Asia reported a 20% increase in container handling speed after retrofitting its RTG cranes with anti-sway systems. The reduction in operator fatigue and cargo collisions also resulted in a 30% decrease in maintenance costs over the following year. These measurable gains have encouraged the terminal to adopt anti-sway systems for all new cranes moving forward.
Conclusion
As container terminals strive for greater efficiency, safety, and automation, anti-sway systems are becoming indispensable. These systems not only mitigate one of the most common hazards in crane operations but also unlock the full performance potential of container gantry cranes. By integrating smart anti-sway technology, ports can achieve faster container throughput, reduced operational risks, and long-term cost savings.
Whether for new crane purchases or retrofits of existing equipment, investing in anti-sway systems is a strategic move that benefits both operations and personnel. As port operations become more digital and data-driven, anti-sway systems will continue to play a central role in the modernization of global logistics.
Comments