How Modern Control Systems Reduce Downtime in Heavy Duty Gantry Crane Use
- charlespsnow
- Jul 2
- 4 min read
In industries where heavy duty gantry cranes are essential to daily operations—such as shipping ports, precast concrete yards, steel mills, and manufacturing facilities—downtime is not just an inconvenience; it’s a costly disruption. Every minute a crane is inoperative, productivity slows, deadlines are missed, and revenue is lost. Modern control systems have emerged as a transformative solution to this issue, significantly reducing downtime through advanced technology, automation, and smarter diagnostics. In this article, we explore how these systems enhance crane reliability, safety, and performance.
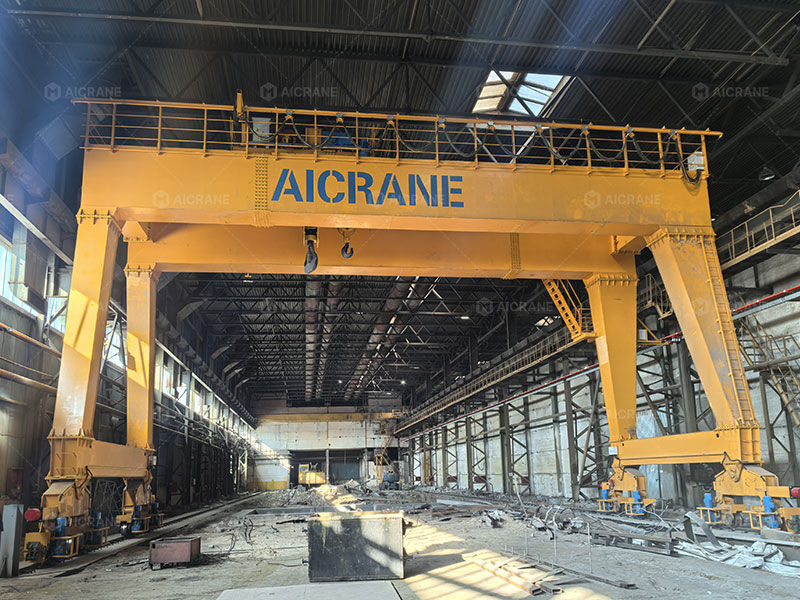
The Downtime Dilemma in Heavy Duty Crane Operations
Heavy duty gantry cranes perform critical lifting and transport tasks for large and bulky loads. However, traditional crane systems can suffer from issues such as:
Mechanical failures due to wear and tear
Electrical system malfunctions
Lack of predictive maintenance alerts
Operator errors
Delayed fault detection and troubleshooting
All of these contribute to unplanned downtime, sometimes requiring hours or even days to resolve—especially in remote or high-throughput industrial sites.
Modern control systems tackle these challenges head-on with smarter control logic, remote monitoring, real-time diagnostics, and automation capabilities.
Key Features of Modern Gantry Crane Control Systems
Modern control systems go beyond basic crane control. They incorporate a wide range of technologies designed to prevent failure, alert operators in real time, and make maintenance more efficient. These systems often include:
Programmable Logic Controllers (PLCs)
Human Machine Interfaces (HMI)
Remote monitoring and diagnostics
Variable Frequency Drives (VFDs)
Condition Monitoring Systems
Anti-sway and positioning controls
Integrated safety and overload protection
Let’s explore how these features work together to reduce downtime in practice.
1. Real-Time Fault Detection and Diagnostics
A major cause of downtime is the time it takes to detect and diagnose a fault. Modern heavy duty gantry crane control systems feature real-time diagnostics through sensors and PLCs. These systems:
Monitor motor temperature, brake performance, gear alignment, oil levels, and vibration
Detect deviations from normal parameters
Trigger alarms or automatically shut down operations to prevent serious failures
The HMI displays error messages and detailed diagnostics, allowing maintenance teams to identify and address issues without dismantling the crane or conducting time-consuming manual checks.

2. Predictive Maintenance Through Condition Monitoring
Traditional maintenance is often reactive—performed after a breakdown. With modern control systems, cranes can utilize condition monitoring to enable predictive maintenance, which includes:
Monitoring key wear indicators such as bearing temperature, motor currents, and oil contamination
Logging operational cycles and usage data
Sending alerts when components approach predefined thresholds
By identifying problems before they result in system failure, users can plan maintenance proactively, schedule downtime during low-load periods, and prevent unexpected outages.
3. Remote Monitoring and Troubleshooting
Many modern gantry cranes are equipped with remote access capabilities, allowing supervisors, OEM engineers, or third-party technicians to access the crane’s control system via a secure internet connection. This allows for:
Remote system diagnostics and software updates
Immediate response to alarms or system warnings
Expert-level support without the need for travel
This dramatically reduces service response time and can often prevent the need for onsite visits entirely.
4. Automation and Error Reduction
Human error is a frequent contributor to downtime. Advanced control systems mitigate this risk with automation features such as:
Automated lifting and lowering sequences
Predefined path programming and trolley positioning
Anti-sway systems that minimize load oscillation
Collision avoidance systems using sensors and interlocks
By reducing operator input in complex or repetitive lifting tasks, automation minimizes the chance of accidents or misalignment that can halt operations.
5. Integration with Terminal and Warehouse Management Systems
In ports, logistics yards, and warehouses, heavy-duty gantry cranes increasingly work in coordination with Terminal Management Systems (TMS) or Warehouse Management Systems (WMS). Through integration, cranes can receive automated job orders, optimized load paths, and location tracking.
Benefits include:
Faster decision-making and load handling
Fewer manual inputs and miscommunication delays
Seamless coordination with AGVs, forklifts, and other machinery
This holistic approach eliminates inefficiencies that lead to downtime.
6. Adaptive Speed Control for Load Efficiency
Variable Frequency Drives (VFDs), a staple of modern crane control, enable adaptive speed control for hoisting, trolley travel, and gantry movement. VFDs:
Adjust speed based on load weight and travel distance
Smooth out acceleration/deceleration, reducing mechanical shock
Extend component lifespan by avoiding sudden starts/stops
Longer-lasting components and smoother operations directly translate to fewer breakdowns and reduced downtime.
7. Enhanced Safety Interlocks
Advanced control systems also embed intelligent safety interlocks that not only improve safety but help avoid shutdowns caused by misuse or unsafe conditions. Features include:
Load moment indicators to prevent overloading
Safe zone restrictions based on geofencing
Redundant safety logic in case of system failure
These safety mechanisms prevent critical incidents that would result in extended operational halts.
Case Example: Reducing Downtime with a Modern Control Upgrade
A steel processing facility operating a 50-ton double girder gantry crane reported frequent unplanned stops due to electrical overloads and hard-to-trace malfunctions. After upgrading the control system to a PLC-HMI architecture with condition monitoring and VFDs, the crane’s average downtime was reduced by over 60%.
Maintenance teams were alerted earlier about wear in motor brushes, operators could visualize real-time crane status, and remote diagnostics allowed for software updates without site visits. As a result, overall plant productivity increased by nearly 15%.
Conclusion: A Smart Investment for Long-Term Gains
While upgrading to a modern control system involves upfront investment, the returns are significant. Heavy duty gantry crane users benefit from:
Dramatically reduced downtime
Longer equipment life
Safer and more reliable operations
Lower maintenance costs
Higher productivity across lifting processes
At a time when efficiency and operational reliability are essential to staying competitive, modern gantry crane control systems are not a luxury—they’re a necessity. Whether for a port authority, construction yard, or steel mill, upgrading control systems is one of the most effective ways to improve uptime and performance.
Comments