How to Choose Motor Power Based on Overhead Crane Capacity Requirements
- charlespsnow
- May 14
- 4 min read
Selecting the right motor power for an overhead crane is crucial to ensure safety, efficiency, and durability of operations. Overhead cranes are widely used in various industries—from manufacturing and assembly plants to steel mills and logistics warehouses—for lifting and transporting heavy loads. One of the critical design elements of any overhead crane system is its motor, which drives lifting, trolley movement, and bridge travel.
Choosing the correct motor power involves more than just matching the crane's lifting capacity. It requires careful consideration of factors such as duty cycle, lifting height, hoisting speed, load characteristics, control methods, and environmental conditions. This article provides a comprehensive guide on how to determine the appropriate motor power based on overhead crane capacity requirements.

Understanding Crane Capacity and Motor Power Relationship
Crane capacity refers to the maximum weight that a crane can lift safely. Motor power, typically measured in kilowatts (kW) or horsepower (HP), determines the ability of the crane to perform work under load. While higher capacity cranes usually require more powerful motors, the exact power requirement depends on multiple interrelated factors.
In general, there is no fixed “one-size-fits-all” formula to determine motor power solely from capacity. Instead, engineers use calculations that consider mechanical efficiency, lifting speed, and duty class to select the optimal motor.
Key Factors That Influence Motor Power Selection
1. Crane Lifting Capacity
The lifting capacity directly affects the size of the hoisting mechanism, which includes the motor, gearbox, drum, and wire rope. As the capacity increases, the motor must generate more torque to lift heavier loads. For example:
A 5 ton overhead crane may require a motor between 3–7.5 kW depending on the lifting speed.
A 20-ton crane typically uses motors ranging from 15–30 kW.
A 50-ton crane might need motor power in excess of 45 kW.
These figures vary based on crane configuration and application.
2. Lifting Height and Speed
The lifting height refers to how far the crane must raise a load, while hoisting speed is how quickly it lifts the load. Faster lifting speeds and taller lifting heights demand greater motor power to maintain performance without overheating or overloading.
For example, lifting a 10-ton load at 8 m/min requires a significantly more powerful motor than lifting the same load at 4 m/min.
3. Duty Cycle and Work Class
The duty cycle refers to how often and how long the crane operates. It’s defined by the crane classification system (FEM or ISO standards), which categorizes cranes from light (A1-A3) to heavy-duty (A6-A8). Heavy duty overhead crane classes demand motors with better thermal capacity and more robust designs.
Light duty (e.g., maintenance shops): Lower power motors with basic insulation are adequate.
Heavy duty (e.g., steel plants, shipyards): Motors need higher power ratings and continuous operation capability.
4. Mechanical Efficiency
Not all power generated by the motor is transmitted directly to lifting. Friction losses in gearboxes, couplings, and wire ropes reduce the effective lifting force. Mechanical efficiency, typically 85–95%, must be factored into motor power selection to ensure the motor compensates for energy losses.
5. Crane Type and Configuration
Different types of overhead cranes—single girder, double girder, underslung, or top running—affect motor requirements. For example, a double girder crane with a trolley-mounted hoist will generally require a more powerful motor than a single beam crane with a fixed hoist.
Moreover, traveling motors for bridge and trolley movements must be sized based on the crane’s weight, acceleration/deceleration, and runway length.
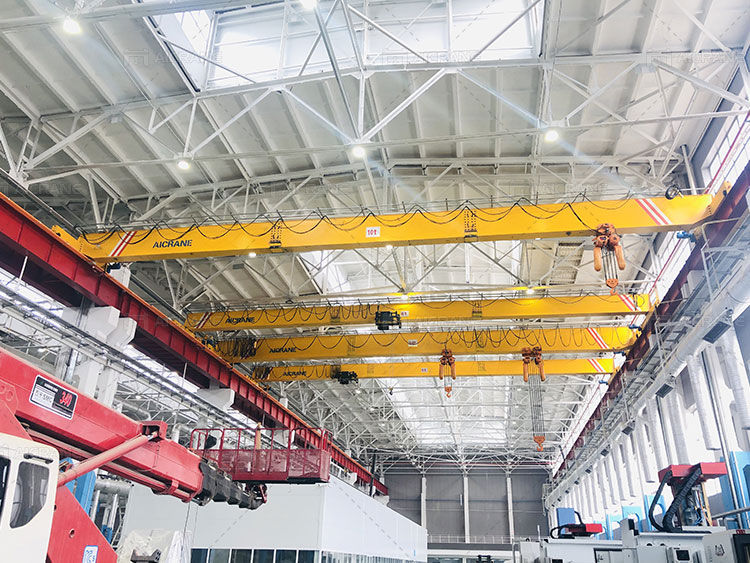
General Steps to Determine Motor Power
Step 1: Calculate Required Lifting Force
Use the following formula:
Lifting Force (N) = Load Weight (kg) × Gravity (9.81 m/s²)
Example: For a 10,000 kg load:
Lifting Force = 10,000 × 9.81 = 98,100 N
Step 2: Determine Power Requirement
Power (W) = Lifting Force × Lifting Speed (m/s)
If you’re lifting 10,000 kg at 6 m/min (0.1 m/s):
Power = 98,100 × 0.1 = 9,810 W or approximately 9.8 kW
Then, factor in mechanical efficiency. If efficiency is 90%:
Required Motor Power = 9.8 kW / 0.90 ≈ 10.9 kW
Round up and select a motor rated for 11–15 kW based on duty cycle.
Step 3: Apply Duty Class Adjustment
If the crane operates continuously, use a motor rated 20–30% higher than the base requirement to accommodate thermal and operational stresses.
Motor Types for Overhead Cranes
1. Squirrel Cage Induction Motors
Commonly used for hoisting and traveling due to their ruggedness and low maintenance.
2. Slip Ring Motors
Used for large capacity cranes requiring high starting torque.
3. Variable Frequency Drive (VFD) Motors
Enable speed control, smooth acceleration, and energy savings. Ideal for cranes with variable speed requirements.
4. Servo Motors
Used in precision applications where exact load positioning is critical, but not common in standard industrial cranes.
Real-World Motor Power Examples Based on Crane Capacity
Crane Capacity | Lifting Speed | Typical Motor Power Range | Application |
5 tons | 5–8 m/min | 3–7.5 kW | Workshop/warehouse |
10 tons | 6–10 m/min | 7.5–15 kW | Factory floor |
20 tons | 6–12 m/min | 15–30 kW | Steel mill, assembly lines |
50 tons | 4–8 m/min | 45–75 kW | Construction, precast yard |
100 tons | 3–6 m/min | 90–150 kW | Heavy equipment lifting |
Other Considerations
Environmental Factors
Motors should be rated for the ambient temperature, humidity, and dust levels. In harsh environments like steel plants or outdoor yards, motors with high IP ratings and heat-resistant insulation are necessary.
Braking Systems
Motors often work in tandem with braking systems to control load descent and prevent overspeed. Choosing a motor with integrated braking capability or compatibility with external brakes is essential.
Redundancy and Safety
For critical lifting tasks, dual-motor systems may be used to ensure redundancy. Always select motors that comply with local safety standards and crane design codes.
Conclusion
Choosing the right motor power for an overhead crane involves more than matching it with the crane's capacity. It requires a holistic analysis of lifting speed, duty cycle, efficiency, and application conditions. By carefully evaluating these parameters, you can ensure your crane system operates safely, efficiently, and cost-effectively.
When in doubt, consult with experienced crane engineers or manufacturers who can provide customized motor selection based on your specific project needs. Investing in the right motor from the start can significantly reduce downtime, energy costs, and maintenance in the long run.
Comments