How to Ensure Safe Operation of Steel Mill Ladle Cranes in Hazardous Environments
- charlespsnow
- Apr 16
- 5 min read
Steel mills are complex, high-risk environments where heavy machinery plays a vital role in the production process. One such critical piece of equipment is the ladle crane, used for transporting molten metal between the furnace, ladle, and casting areas. Due to the hazardous nature of molten metal and the extreme operating conditions, ensuring the safe operation of ladle cranes in these environments is paramount.
In this article, we will discuss essential safety measures and best practices for operating ladle cranes safely in steel mills, focusing on minimizing risks, maintaining equipment, and training personnel to handle potential hazards effectively.

Understanding the Risks Involved
Before we dive into safety measures, it's essential to understand the risks associated with ladle crane operations in a steel mill:
Molten Metal Exposure: Ladle cranes often handle molten metal at temperatures exceeding 1,500°C (2,732°F). Even a slight mishap or equipment failure can result in dangerous spills or splashes, which can cause severe burns or fires.
High Heat Environments: The extreme temperatures not only pose a risk of burns but also cause metal fatigue in the crane’s components, leading to mechanical failures if the equipment is not properly maintained or rated for such conditions.
Heavy Loads: Ladle cranes are designed to lift and transport extremely heavy loads, including the ladles themselves, which can weigh up to hundreds of tons when filled with molten metal. Overloading or improper handling of these loads can lead to structural failure or tipping.
Corrosive Environments: Steel mills use a variety of chemicals and materials that can corrode crane components over time. Exposure to molten metal, slag, and other byproducts of the steelmaking process requires regular inspections and the use of corrosion-resistant materials.
Electrical and Mechanical Failures: Ladle cranes are equipped with complex electrical and mechanical systems that, if not properly maintained or monitored, can fail, potentially causing accidents.
Given these risks, taking proactive measures to ensure safety is crucial.
1. Proper Equipment Design and Maintenance
A fundamental aspect of safe ladle crane operation is ensuring that the equipment is designed and built to handle the extreme conditions of the steel mill environment.
Ladle Crane Design: The crane’s components, such as hoists, ropes, hooks, and controls, should be constructed from high-strength, heat-resistant materials. This is especially important for components that come into direct contact with molten metal or exposed to high temperatures.
Temperature Resistance: Use materials designed to withstand high temperatures and thermal stresses. For example, high-performance steel alloys, heat-resistant coatings, and flameproof motors can help minimize heat-related wear and tear on the steel mill crane.
Corrosion Protection: Galvanized components or cranes with corrosion-resistant coatings are essential to protect against the corrosive effects of molten slag, chemicals, and humidity present in the steel mill environment.
Preventive Maintenance: Establish a routine preventive maintenance program that includes daily, weekly, and monthly checks on critical components like the hoist, lifting hook, wire ropes, and crane control systems. Regular lubrication of moving parts and inspection for wear and tear help prevent mechanical failures.
Temperature Monitoring Systems: Temperature sensors and monitoring systems should be installed on critical crane components to ensure they are not overheating, which could result in equipment failure.
2. Safety Features for Hazardous Conditions
Ladle cranes should be equipped with safety features that protect both operators and the equipment. These features may include:
Overload Protection: Overload sensors and weight monitoring systems should be integrated into the crane’s control system. These systems can prevent the crane from operating if it is carrying an excessive load, which could strain the crane’s structure or cause tipping.
Emergency Shut-Offs and Backup Systems: Install emergency stop buttons at various points around the crane’s control system, including remote controls. Additionally, redundant systems for critical functions, such as backup motors and power supplies, ensure that the crane can still operate safely in the event of an emergency.
Fire Suppression Systems: Given the presence of molten metal and the high temperatures, fire suppression systems—such as automatic sprinklers, foam systems, or CO2 extinguishers—should be installed on and around the crane. These systems can help contain a fire before it spreads.
Automatic Load Monitoring: Ladle cranes should be fitted with automatic load monitoring devices that track the weight of the ladle being transported. These devices prevent overloading, which could cause crane failure or instability.
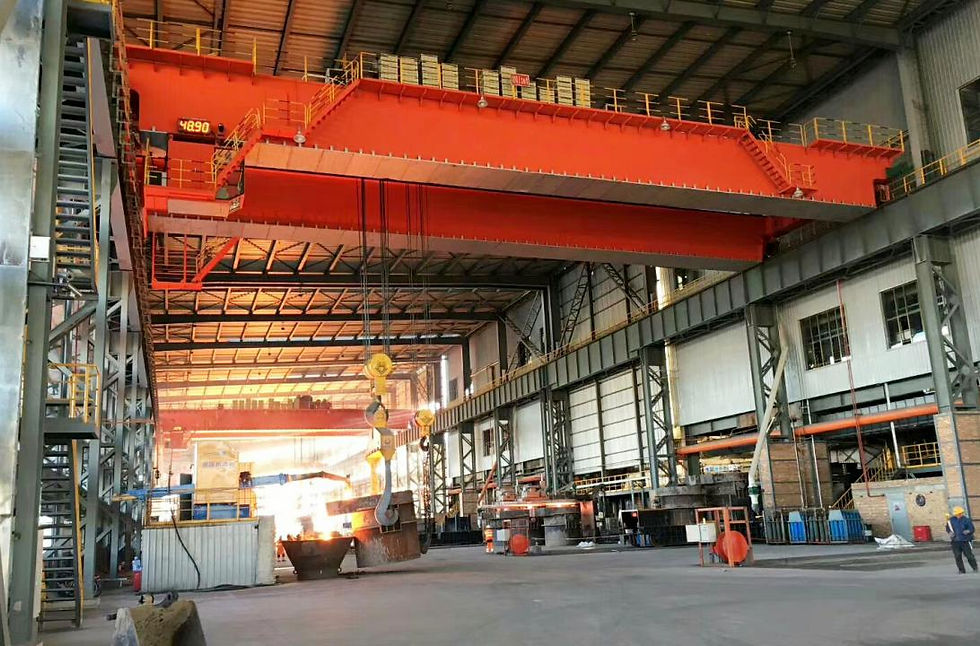
3. Operator Training and Competence
Training is one of the most critical aspects of ensuring the safe operation of ladle cranes in hazardous environments. Operators must be skilled and knowledgeable about both the crane’s capabilities and the risks involved in handling molten metal and operating in high-temperature conditions.
Crane Operation Training: Operators should undergo comprehensive training that covers both theoretical and practical aspects of ladle crane operation. They must understand the crane’s capabilities, including load limits, the importance of smooth lifting and lowering motions, and proper load alignment.
Hazardous Environment Training: Given the nature of steel mills, operators should be trained to handle the unique risks associated with molten metal handling. This includes understanding emergency procedures, such as how to react in case of a spill or fire, as well as how to use safety equipment, including flame-resistant clothing and heat protection gear.
Emergency Response Drills: Conduct regular emergency response drills to prepare operators for real-life situations. These drills should simulate various emergency scenarios, including molten metal spills, equipment failures, and fire outbreaks, ensuring that operators know how to act quickly and effectively in an emergency.
Continuous Education: Steel mills and ladle crane operators should participate in ongoing education and training programs to stay current with the latest safety standards, technological innovations, and best practices.
4. Monitoring and Control Systems
Modern ladle cranes should be equipped with advanced monitoring and control systems that provide real-time data on crane performance, load conditions, and environmental factors.
Load Tracking and Diagnostics: Real-time load tracking systems allow operators and supervisors to monitor the weight of the ladle, load distribution, and other critical parameters. This system can send alerts if the crane is nearing its load capacity or operating outside safe limits.
Remote Control and Automation: Remote operation of ladle cranes can be employed to ensure that operators maintain a safe distance from the crane’s movements, reducing the risks of exposure to molten metal. Automated control systems can also optimize crane movements, ensuring smooth and precise operations.
Data Logging and Reporting: Automated data logging systems can track crane performance, maintenance history, and operational incidents. This data is invaluable for identifying trends and potential areas for improvement in this heavy duty overhead crane safety.
5. Safety Protocols and Standard Operating Procedures
Steel mills must establish clear, comprehensive safety protocols and standard operating procedures (SOPs) to guide ladle crane operation. These protocols should be developed with input from safety experts and operational personnel and cover:
Pre-Operation Checks: Before beginning operations, operators should conduct thorough inspections of the crane, checking for signs of wear, mechanical issues, or hazards. Any malfunction should be reported, and the crane should be taken out of service for repair.
Clear Communication: A robust communication system should be in place to ensure clear and constant communication between crane operators, floor supervisors, and other personnel working in the mill. This includes the use of radios, signals, and visual indicators.
Post-Operation Inspections: After each use, operators should inspect the crane to ensure that it has not sustained damage during operation. Any issues should be documented and addressed promptly.
Conclusion
Ensuring the safe operation of steel mill ladle cranes in hazardous environments requires a combination of well-designed equipment, advanced safety features, comprehensive operator training, and robust monitoring systems. Steel mill managers must take a proactive approach to mitigate the inherent risks associated with handling molten metal, extreme temperatures, and heavy loads. By implementing these safety measures, operators can minimize the likelihood of accidents, protect personnel, and ensure smooth and efficient steel production operations.
Comments