How to Troubleshoot Common Container Gantry Crane Parts Failures
- charlespsnow
- Mar 26
- 5 min read
Container gantry cranes are essential for the efficient handling and transportation of containers in ports and other industrial settings. These machines are complex and operate under high loads and challenging environmental conditions, making them prone to mechanical and electrical failures. When a component of the crane malfunctions, it can lead to delays, safety hazards, and costly repairs. In this article, we’ll explore common container gantry crane parts failures and provide a step-by-step guide to troubleshooting these issues.
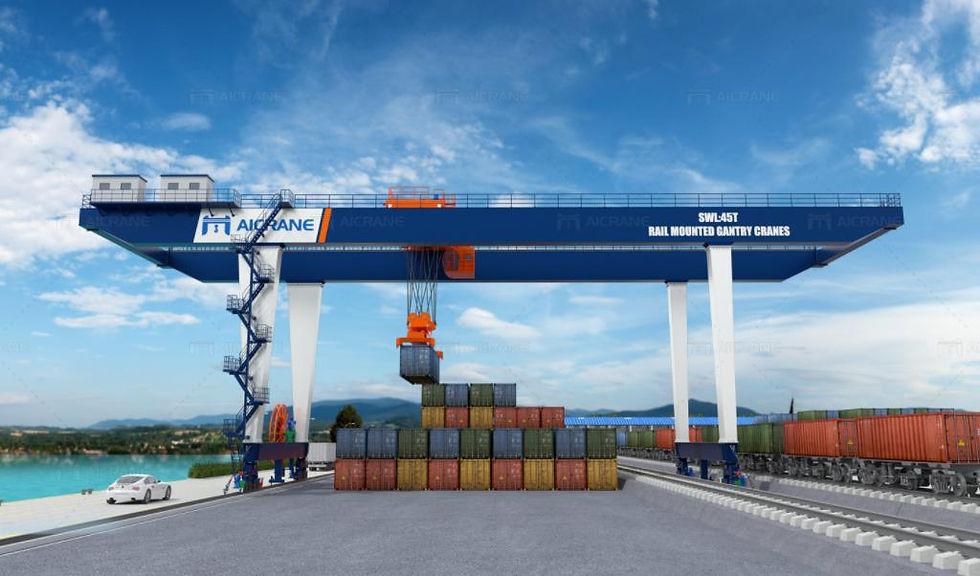
Understanding Container Gantry Cranes
Before diving into troubleshooting, it’s important to understand the basic structure of a container gantry crane. These cranes are typically used to lift and move containers from ships to trucks or railcars. They consist of several key components, including:
Main girder: The horizontal structure that supports the load.
Trolley and hoist: The trolley moves along the girder, carrying the hoist mechanism responsible for lifting the load.
Rails: The gantry crane moves along rails to position itself over containers.
Control system: The system used to operate and control the crane, typically involving a cabin, remote control, or automated system.
Failures in any of these parts can result in a significant operational impact, but with proper troubleshooting procedures, these issues can often be resolved quickly and effectively.
1. Hoisting Mechanism Failures
The hoisting mechanism is a crucial part of the crane that allows for lifting and lowering containers. Common hoisting problems include:
a. Lifting Speed Issues
If the lifting speed is slower than usual, this could be caused by:
Power supply problems: Ensure that the crane is receiving the correct voltage. A voltage drop can slow down the lifting speed.
Overloaded hoist: Verify that the crane is not lifting more than its rated capacity. Overloading can cause the motor to strain and slow down.
Worn-out motor or gearbox: Over time, the motor or gearbox may wear out, leading to inefficient operation.
Troubleshooting Steps:
Inspect the power supply for consistency and ensure the voltage matches the gantry crane specifications.
Verify the load being lifted does not exceed the crane's capacity.
Perform a visual inspection of the motor, gearbox, and other components for signs of wear and tear.
b. Lifting Won't Start
If the hoisting mechanism doesn't start when commanded, this could be due to:
Electrical circuit failure: A fault in the control panel or wiring could prevent the lifting mechanism from operating.
Brake failure: The brakes may be engaged or malfunctioning, preventing the lifting motion.
Troubleshooting Steps:
Check the crane’s electrical system and fuses for faults.
Test the control system to ensure there is no issue with the signals being sent to the motor.
Check the brake mechanism for malfunctions or excessive wear.
2. Trolley Movement Issues
The trolley, which moves along the crane’s main girder, is responsible for positioning the hoist over containers. Common issues with trolley movement include:
a. Jerky or Uneven Movement
Uneven or jerky movement could be caused by:
Damaged rails: Over time, the rails may become damaged due to constant use or environmental conditions.
Worn-out wheels: The wheels of the trolley may wear unevenly, causing irregular movement.
Improper alignment: Misalignment of the trolley tracks can lead to uneven movement.
Troubleshooting Steps:
Inspect the rails for damage or signs of wear. Ensure they are level and free of debris.
Check the trolley wheels for wear and replace them if necessary.
Inspect the alignment of the trolley tracks and adjust them if needed.
b. Trolley Won't Move
If the trolley refuses to move, the potential causes could include:
Power failure: A lack of electrical power to the trolley motor can prevent movement.
Control system failure: Malfunctions in the control system, such as faulty sensors or circuit boards, could cause the trolley to stop functioning.
Troubleshooting Steps:
Check the electrical system supplying the trolley motor.
Inspect the control system, including sensors, switches, and wiring, for faults.
Test the trolley’s motor for proper operation.
3. Braking System Failures
The braking system ensures that the crane halts safely when needed. Failures in the braking system can be critical to both safety and functionality.
a. Brake Slippage
Brake slippage occurs when the brakes fail to hold the crane's load securely. Common causes include:
Worn brake pads: Over time, brake pads may wear down, reducing their effectiveness.
Hydraulic fluid leaks: If the braking system relies on hydraulic power, a fluid leak can cause a drop in pressure, leading to brake slippage.
Troubleshooting Steps:
Inspect the brake pads for wear and replace them if necessary.
Check the hydraulic system for leaks and ensure that the fluid level is adequate.
Test the brake system to ensure proper pressure and function.
b. Brakes Won't Release
If the brakes do not release when the crane is in motion, this could be due to:
Faulty brake release mechanism: A malfunction in the release mechanism, such as the air or hydraulic lines, can prevent the brakes from disengaging.
Brake overheating: Overuse of the brakes can lead to overheating, causing the system to lock up.
Troubleshooting Steps:
Inspect the brake release mechanism for faults or blockages.
Check the brake temperature to ensure it is not overheating.
Test the braking system for proper release functionality.
4. Control System Failures
The control system is the brain of the container gantry crane, responsible for translating operator commands into actions. Failures in this system can disrupt crane operation and require prompt attention.
a. Unresponsive Control Panel
If the control panel is unresponsive, the potential causes may include:
Power supply issues: Ensure the control panel is receiving power and that the circuit breakers are functioning.
Faulty wiring or connections: A loose or damaged wire can disrupt signals between the control panel and the crane’s components.
Troubleshooting Steps:
Check the control panel’s power supply and inspect the fuses.
Inspect the wiring for loose or damaged connections.
Test the buttons and switches for proper operation.
b. Faulty Remote Control
If the crane is controlled remotely and the remote stops working, the issue could be:
Dead batteries: The remote may simply need new batteries.
Signal interference: Environmental factors or other equipment nearby may be interfering with the signal.
Internal circuit failure: The remote control’s internal circuits may be damaged or malfunctioning.
Troubleshooting Steps:
Replace the batteries in the remote control and test its functionality.
Move the crane away from any potential sources of interference.
Test the remote control’s internal components for signs of failure.
5. Structural Issues
In addition to mechanical components, structural issues can also lead to crane failures.
a. Cracked or Damaged Main Girder
The main girder bears the majority of the crane’s load. If it is cracked or damaged, it can compromise the safety of the crane. The causes can include:
Overloading: Lifting more than the crane’s rated capacity can put excessive stress on the girder.
Fatigue: Repeated use over time can cause fatigue and cracks to form in the metal.
Troubleshooting Steps:
Perform regular visual inspections of the main girder for signs of cracks or wear.
Use non-destructive testing (NDT) methods like ultrasonic or magnetic particle inspections to detect internal cracks.
Ensure the crane is not being overloaded beyond its rated capacity.
Conclusion
Troubleshooting container gantry crane parts failures is a complex task that requires a methodical approach and attention to detail. Regular maintenance, timely inspections, and prompt attention to faults can prevent major issues from escalating. By following the troubleshooting steps outlined above, crane operators and maintenance teams can quickly identify and resolve common failures in hoisting mechanisms, trolley movement, braking systems, control systems, and structural components. This ensures the crane operates efficiently, safely, and with minimal downtime, leading to enhanced productivity and longevity of the equipment.
Comments