Wireless Control and Remote Operation of Overhead Cranes
- charlespsnow
- May 19
- 5 min read
In modern industrial operations, efficiency, safety, and precision are more critical than ever. One of the key technologies transforming material handling and lifting operations is the wireless control and remote operation of overhead cranes. Traditionally operated by pendant controls or cabin operators, overhead cranes have evolved significantly with the integration of wireless technologies. These innovations offer numerous advantages in terms of operator safety, enhanced productivity, and operational flexibility.
This article explores the fundamentals of wireless crane control, its components, benefits, challenges, and practical applications across different industries.
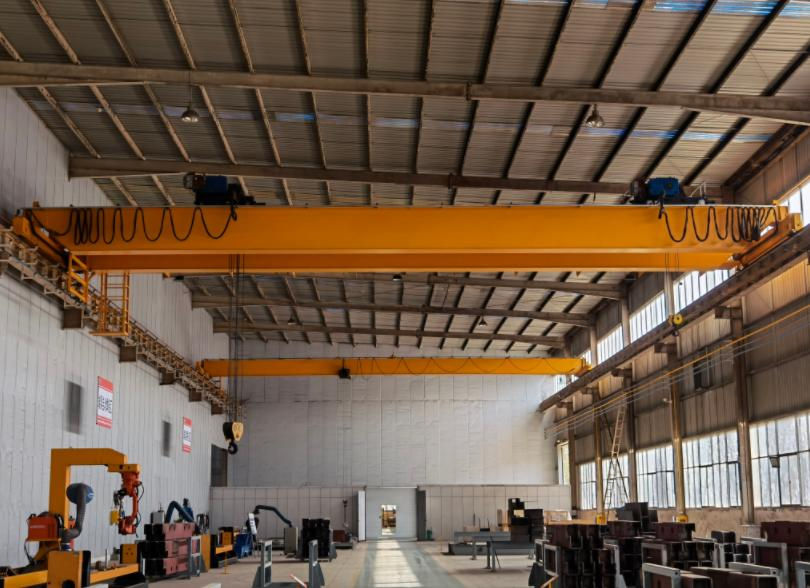
What Is Wireless Control for Overhead Cranes?
Wireless control systems for overhead cranes involve the use of radio remote controls that allow operators to control crane functions from a distance. These systems typically include a transmitter (held by the operator) and a receiver (mounted on the crane). Through encoded radio signals, the transmitter communicates commands such as lifting, lowering, traveling, and trolley movement to the remote control overhead crane.
Wireless remote systems can be designed for simple single-speed cranes or more complex variable-frequency drive (VFD) systems that allow for fine control of movement and positioning.
Key Components of a Wireless Crane Control System
Transmitter (Remote Control):The handheld device used by the crane operator to issue commands. It usually includes push buttons, joysticks, and indicators for various crane motions.
Receiver Unit:Installed on the crane itself, the receiver decodes the radio signals sent by the transmitter and activates the crane's motors or control circuits accordingly.
Antenna System:Ensures reliable communication between the transmitter and the receiver, even in complex environments like warehouses or manufacturing facilities.
Battery System:Both the transmitter and receiver units may be powered by rechargeable or replaceable batteries to ensure uninterrupted operation.
Safety Systems:Most wireless systems include safety features such as emergency stop buttons, automatic frequency hopping, and fail-safe protocols to prevent accidents or interference.
Advantages of Wireless Control and Remote Operation
1. Enhanced Safety
One of the most compelling reasons to adopt wireless control is improved safety. Operators no longer need to stand close to heavy loads or dangerous machinery. Instead, they can operate the crane from a safe distance, avoiding hazards such as falling materials, high-voltage areas, or extreme temperatures.
2. Increased Operator Mobility
With wireless control, operators can move around freely and select the best vantage point for viewing and managing crane operations. This flexibility leads to more accurate load positioning and fewer errors during lifts.
3. Reduced Operator Fatigue
Cab-operated cranes require operators to stay in the crane cabin for extended periods, which can lead to fatigue. Wireless remote controls allow ground-level operation, which is generally more ergonomic and less physically demanding.
4. Greater Productivity
Wireless controls eliminate the need for an additional spotter or signalman. The operator can handle the eot crane independently, streamlining operations and reducing labor costs.
5. Lower Installation and Maintenance Costs
Compared to fixed pendant systems, wireless controls reduce the need for extensive wiring, tracks, or suspensions. This not only saves on installation costs but also minimizes maintenance issues related to cable wear and tear.
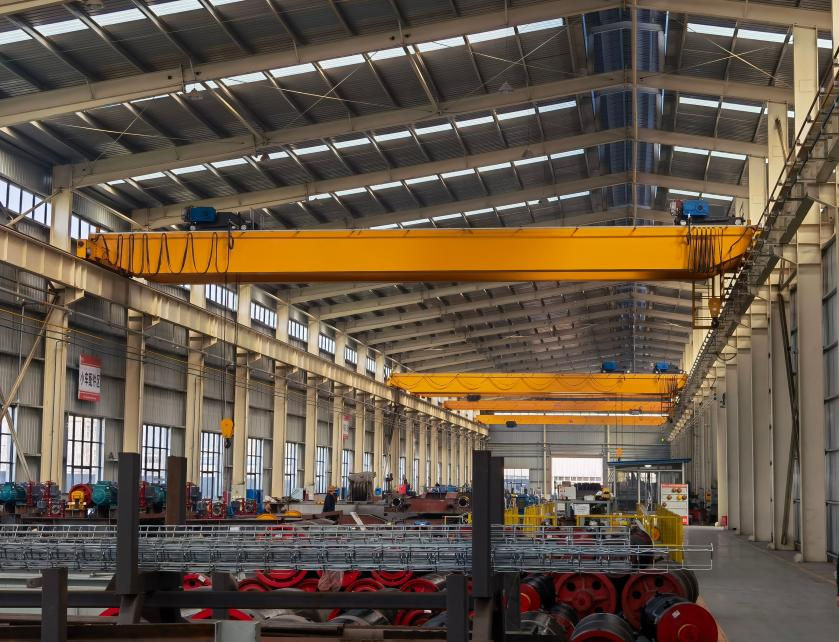
Challenges and Considerations
1. Interference and Signal Loss
One of the primary concerns with wireless systems is potential signal interference, especially in industrial environments filled with electronic devices. However, modern remote systems use frequency-hopping spread spectrum (FHSS) technology to avoid interference and maintain secure communication.
2. Battery Management
Wireless transmitters and receivers depend on battery power. Proper battery maintenance, including regular charging and timely replacement, is essential to avoid unexpected downtimes.
3. Initial Cost
The upfront cost of a high-quality wireless control system may be higher than traditional wired systems. However, the investment is typically offset by long-term savings in labor, maintenance, and productivity improvements.
4. Training Requirements
Operators need adequate training to safely and effectively use wireless crane controls. While the learning curve is usually short, it’s crucial that personnel are familiar with safety protocols and emergency procedures.
Common Applications of Wireless Crane Operation
1. Steel Mills and Foundries
In environments where high heat, dust, and radiation pose safety risks, wireless controls allow foundry crane operators to stay at a safe distance while maintaining precise control of heavy loads like molten metal ladles or steel coils.
2. Warehousing and Logistics
Overhead cranes used in logistics hubs or warehouses benefit greatly from wireless controls, enabling operators to move around the storage area to find the best angles and avoid collisions during material handling.
3. Manufacturing Plants
Assembly lines and production facilities often require quick and repetitive movements. Wireless remote control systems enable fast, accurate lifting operations without interrupting workflow.
4. Shipyards and Ports
In marine environments, the ability to control cranes remotely is invaluable for loading and unloading cargo, as well as for working on large ship components or containers.
5. Maintenance and Repair Operations
Cranes used in maintenance work often need to navigate tight spaces or hazardous zones. Wireless control allows technicians to maintain visual contact with the load while staying out of harm’s way.
Types of Wireless Remote Controls
Wireless control systems vary in complexity depending on crane size and application:
Basic Push-Button Remotes:Suitable for light-duty cranes or basic hoisting tasks. Typically include directional buttons for up/down and left/right movement.
Joystick Controls:Provide more precise control and are ideal for larger cranes handling heavy loads or requiring variable speed movement.
Custom Programmable Remotes:Offer advanced features such as load feedback, automatic load detection, multi-crane control, and integration with SCADA or PLC systems.
Regulatory and Safety Standards
Wireless crane operations must comply with industry safety regulations, such as:
ISO 13849 – Safety of machinery: Safety-related parts of control systems
EN 60204-32 – Electrical equipment of hoisting machines
OSHA Guidelines (U.S.) – Standards for crane operator safety
FEM (European Materials Handling Federation) – Provides recommendations for radio remote controls in cranes
Following these standards ensures system reliability and operator protection.
Future Trends in Wireless Crane Control
The future of wireless crane operation is leaning toward automation, IoT integration, and data-driven maintenance. Emerging technologies include:
Smart Remotes with touchscreens and load monitoring feedback
Integration with fleet management systems for real-time usage data
AI-powered load control systems for automatic obstacle detection
Remote diagnostics for predictive maintenance and system health checks
As the industrial world moves toward Industry 4.0, wireless crane systems will become smarter, safer, and more efficient.
Conclusion
Wireless control and remote operation of overhead cranes mark a significant advancement in industrial lifting technology. By removing the operator from hazardous zones, enhancing mobility, and enabling precise load handling, these systems contribute to a safer, more productive workplace. While the technology requires a solid understanding of proper usage, battery care, and signal management, its benefits far outweigh the challenges.
Companies investing in wireless crane controls are positioning themselves for more agile, scalable, and cost-effective operations—setting the foundation for smarter material handling in the years to come.
Comments